BLOG
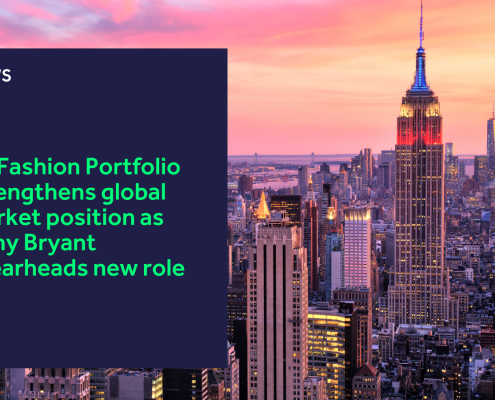
BLOG
The term “fashion industry” is a broad umbrella comprising multiple sub-verticals that people often don’t consider. One such example is workwear.
It is well known that companies have dedicated uniforms that employees must wear, but seldom do people think about how these garments are created.
While these items are often produced en masse and distributed to specific clients who handle the embroidery, workwear companies still face a myriad of back-office challenges.
Below, we shine a light on these challenges and offer solutions that workwear companies can utilise.
Workwear fashion companies, much like their counterparts in other fashion verticals, often produce items in multiple variants.
While these may not be as drastic as other fashion brands, the reality is that uniforms must still be produced in various fits.
Furthermore, diversity is still essential to cater to the unique needs of different businesses and industries.
Coordinating the production and availability of these variants without an efficient solution can take significant time, which is a drain on resources. There are solutions, however, that can seamlessly manage products and their respective variants to boost operational efficiency.
Managing inventories for workwear brands is a complex task due to volume. Often, these companies mass-produce uniforms for clients, which can take much work to manage.
Workwear brands must be able to track each item meticulously to ensure they know precisely where each piece is at any given moment.
Without robust inventory management solutions, reputational and financial risks loom large. Accurate tracking is crucial for operational efficiency and meeting the specific demands of clients in this vertical.
The workwear industry contends not only with variant and inventory challenges but also with the laborious task of data entry.
Manual processes consume valuable time that could be redirected towards more strategic endeavours.
Matrix frameworks and advanced solutions streamline data entry, provide real-time stock information, and integrate with product status functionality, allowing for more efficient back-office operations.
Workwear companies typically rely on specific fabrics to create uniforms, such as for firefighters. In these cases, workwear companies are also subject to compliance regulations to meet health and safety standards.
As such, these companies must have stringent checks in place throughout the production cycle.
By implementing such checks into their processes, workwear companies can ensure the uniforms delivered meet the highest standards expected by both businesses and regulatory bodies.
Workwear businesses often produce items for companies across many industries and, in some cases, different countries.
However, as they break into new markets, there are challenges adapting back-office processes to local regulations, tax structures, and cultural nuances.
Managing diverse legal and compliance requirements while maintaining operational consistency demands strategic planning and adaptability.
Additionally, the complexities associated with shipping materials and goods between countries add another challenge that requires tailored solutions.
In navigating these challenges, workwear businesses need solutions that empower them to overcome back-office blockers and drive operational excellence.
K3’s Fashion Solution Portfolio offers concept-to-consumer solutions, embedded in the Dynamics 365 technical infrastructures, that empower companies to streamline variant creation, simplify inventory management, and optimise processes.
If you’d like to learn more about how K3 can support you, feel free to drop us a line today.
Sign up to the Beneath the Drape newsletter to receive fortnightly updates on all the latest and greatest from the K3 Fashion Portfolio!